British stone: Stamford Stone Company says the time for waiting is over
Covid put Stamford Stone’s plans for a new factory workshop on hold following planning approval for a 43-acre extension to Clipsham Bidwells quarry. But now those plans are moving ahead.
See Stamford Stone at:

Inflation and the cost of living crisis might still be hitting the headlines from time to time but companies cannot wait for ever to achieve their ambitions and for Stamford Stone (the name of which is now a registered trade mark) the time has come to move on.
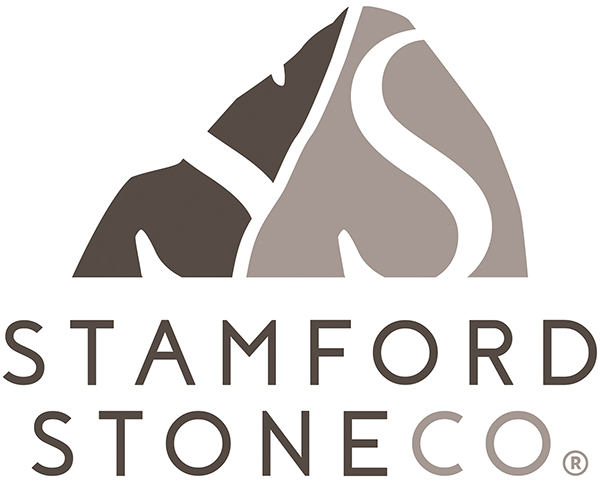
Stamford Stone extracts Clipsham limestone from its Bidwells and Medwells quarries in Clipsham, Rutland. Achieving planning permission for mineral extraction always takes a long time and obtaining it for the 43-acre extension of Clipsham Bidwells quarry was no exception, even though much of the preliminary work had been carried out by the previous owners, Clipsham Quarry Company, before Stamford Stone bought the company, including 300-acres of land and 1,800 acres of mineral reserves, in 2018.

Planning permission was finalised and extraction started in the 43-acre extension in 2021. Although Stamford Stone Company had been able to carry on working throughout the pandemic, due to the nature of its work being mostly in the open air or isolated with machinery, Director Daniel Wilson did not think the past two years were the right time for more investment.
Now, with a bulging order book, he sees no reason for waiting any longer and plans to go ahead with building a new, 7,000m2 factory workshop at Clipsham Bidwells quarry.
In fact, he admits that “had we not been watching the news for the past six months we probably would have cracked on with it already”.
Having a factory in the quarry will mean the raw block will not have to travel 20 miles-or-so to Stamford Stone’s factory and showroom in Helpston to be processed.
That will reduce its carbon footprint, not to mention transport costs – and, when you are transporting raw block, despite much of it already being scanted in the quarries – a proportion of what you are moving is waste. Having a factory in the quarry would mean transporting more finished product.
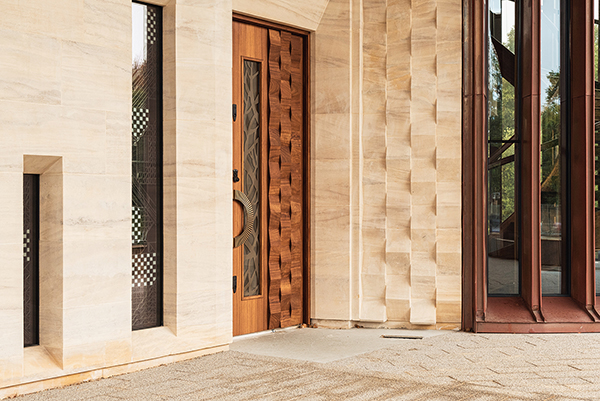
Planning limits how much stone can be moved out of the quarry, and although that limit is fairly high at 170,000 tonnes a year from Clipsham Bidwells quarry, it is preferable to have as much of it as possible leaving as high value finished or semi-finished product, especially as the initial yields from the newly consented area are better than expected.
At the top of the quarry is Bidwell Clipsham, with its distinctive bands. Below that are plainer beds of Lincolnshire limestone, and below that, harder Clipsham Cream, which is currently being used for an elaborate private new-build in London, although Stamford Stone has signed an NDA on that and can’t say anything about it except that it is truly impressive.
Of course, cores were taken from the new area to anticipate the yields but, as Dan says, you never know precisely what you will find until you actually open up a quarry.
Stamford Stone’s plan is to reduce the carbon footprint still further by generating renewable electricity with wind turbines and / or solar panels on about 100 acres of the 300 it bought along with the quarry. It sees another potential carbon benefit from offsetting by extending the existing 70 acres of woodland on the site. It believes it could also help other companies achieve net carbon neutrality by selling offsetting.
Dan says Bidwells quarry could be energy self-sufficient from renewables but had been equivocating about whether to connect to the national grid in order to feed into it and, if necessary, draw from it. But the connection point is not close by and he describes the cost of connection as “astronomical”.
The issue might have been settled by a company that is looking for land on which to put extensive banks of batteries to even out the peaks and troughs of sustainable electricity production. It charges the batteries during peaks and feeds the electricity into the grid during troughs.
Not only would the company pay to house its batteries on Stamford Stone’s land, it would also meet the cost of connecting to the national grid (because it does not have a business without the connection). Dan says it is something other quarry operators might like to look at and he would be happy to talk to them about it.
There is also a new management structure at Stamford Stone. Although the company had continued working during the Covid pandemic, some of the 48 people there were furloughed during the early days and Dan and his sister and fellow Director, Laura Green, got stuck in to even more of the work than usual.
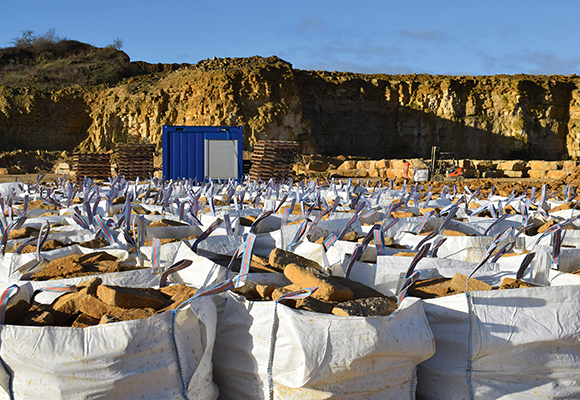
Dan has said previously how beneficial that proved to be by making them aware of some of the inefficiencies of the production process and how they could be improved.
But it also made them aware that they were still running the business as if it employed the 11 people who were there when they took over the day to day running of the business eight years ago. That in itself was less than optimally efficient because they were spending too much time working in the business rather than managing its development.
Consequently, a senior management team has now been developed that sees Tom Arlow in charge of the two quarries assisted by Louisa Turner. Alan Hanrahan has joined the company to add his expertise in logistics as Operations Manager, setting budgets and controlling costs. Tony James is Production Manager at the factory in Helpston with Ricky Parkinson as Plant Maintenance Manager, keeping the company at the forefront with new plant and machinery both in the quarries and in the production facilities. Wendy Ivatt and Richard Hall head the draughting and estimating team, which is expanding due to the amount of large commercial projects the company is now involved in.
More economies might come from building a road between Bidwells and Medwells quarries. That would enable lorries from both to access the A1 without having to go through the village of Stretton, which would help to keep the neighbouring residents happy.
Even though the two quarries are close together, they have differing characteristics and the stones are sold separately and at different price points. Dan says Clipsham Medwells is the best choice for sky facing applications such as cappings.
Block from both quarries is sold to a dozen or so masonry companies and walling and flooring stone is also sold business-to-business, with most of the walling stone sold through builders merchants, especially when it goes to the Cotswolds and further north, such as Harrogate. It is generally white labelled as ‘Lincolnshire stone’ to carry the merchant’s branding.
Although there is a growing commercial imperative to be seen as environmentally friendly, it is something that Dan says he and his family have always tried to achieve.
Carbon reduction has clearly grown in significance, but biodiversity is also an issue and it is often forgotten how many quarries and former quarries are designated Sites of Special Scientific Interest (SSSIs).
At Clipsham Medwells quarry there are significant areas of calcareous grassland that are home to some of the country’s rarer fauna and flora. And there are protected Peregrine falcons nesting in rock faces.
There is no blasting in the quarries and even a factory in Medwells would be inconspicuously within the quarry with minimal noise from the machinery. In fact, Dan currently has planning applications in for off-grid eco-pods for people to escape to, away from technology and modern living, in the original ‘Big Pits Quarry’, which ceased being worked in the 1980s.
Stone from Clipsham Bidwells has taken its place alongside the stone from Clipsham Medwells, and in the product display area at Helpston even sits comfortably alongside the imported stones that Stamford Stone sells for hard landscaping, much of it these days from Morocco and Egypt. The stone is sourced from ethical quarries, says Stamford Stone.
Much of the Clipsham masonry goes to the colleges of Cambridge and Oxford, both for conservation and new build. One of the projects currently taking 400m3 of Clipsham is the new Stephen A Schwarzman Centre for Humanities at Oxford, which resulted from a CPD presentation Stamford Stone gave to the architects at Hopkins three years ago. “We do a lot of CPD presentations,” says Dan. A team from the project, where Vetter Laing O’Rourke is the contractor, visited Clipsham Bidwells quarry to select the blocks wanted well in advance of the start of the construction work.
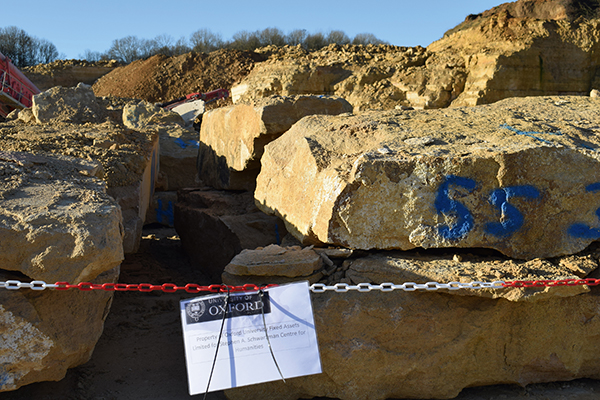
Other Oxford College projects, both with Szerelmey, are at Rhodes House and Corpus Christie, respectively using 40m3 and 70m3 of Clipsham limestone
Right now Stamford Stone is also gearing up for the Natural Stone Show at ExCeL in London in June (you will find the company on stand F56). “We always try to bring quite a lot of project images as well as a great range of samples from both our Clipsham quarries,” says Dan.
With talk of recession now less common than it was at the end of last year, Dan believes he is justified in feeling optimistic. “We’re geared up now for a good time ahead. With some exciting projects, plentiful supply of the finest limestone and a great team of people, we’re excited about the future.”
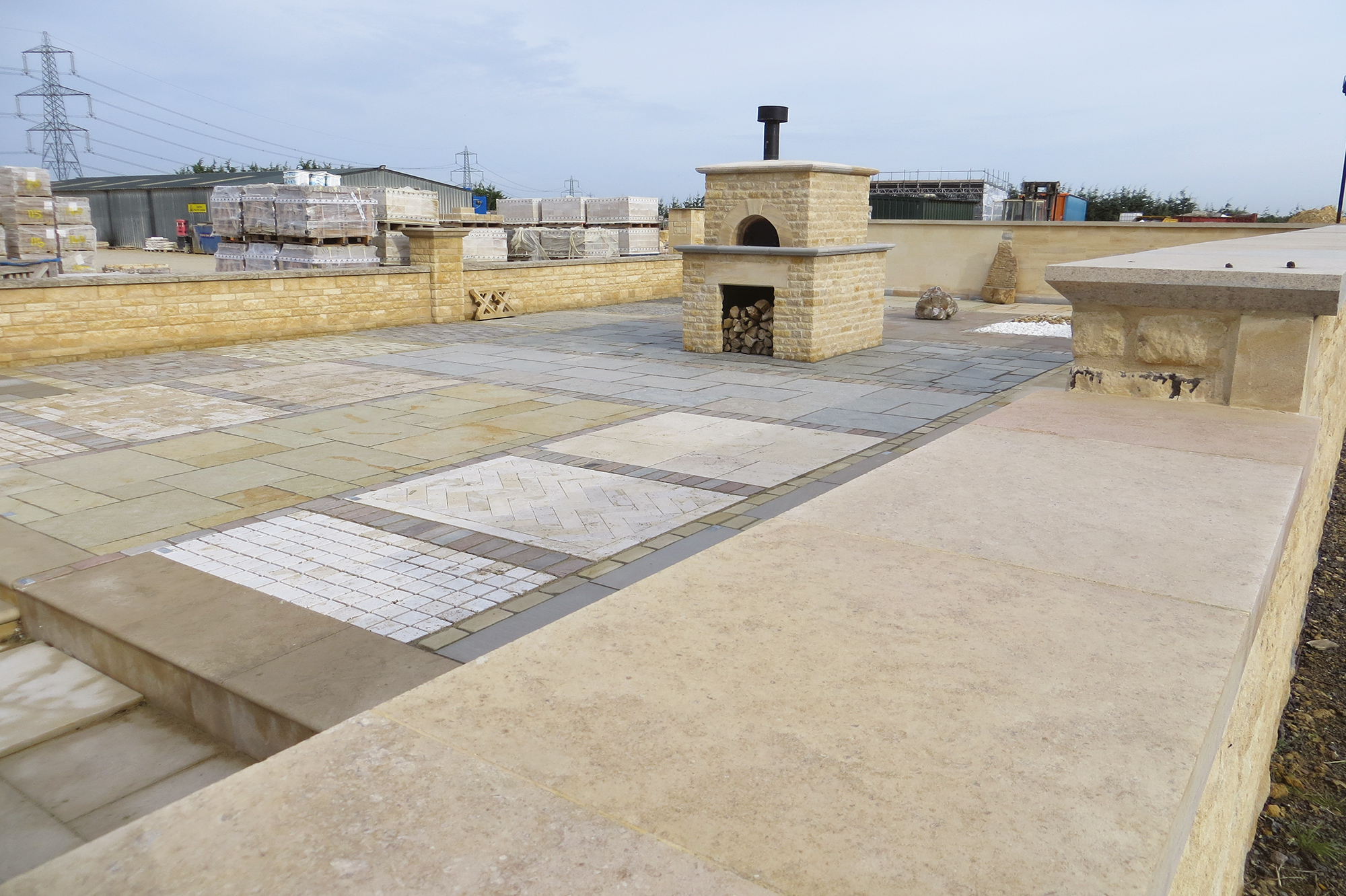
Part of Stamford Stone’s hard landscaping display in Helpston. Hard landscaping is a growing market for the company, with demand for both the stone from its own quarries and stone imported from Morocco and Spain.